Lapping Abrasives / Abrasive Powders
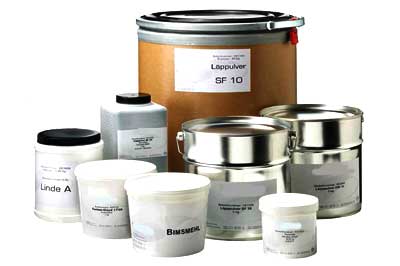
We offer a complete line of lapping abrasive products for processing today's complex materials. For general engineering applications, we offer Aluminum Oxide, Silicon Carbide, Boron Carbide, and Diamond Powder. For high-tech materials, glass, and other polishing applications, we offer Micro-graded Diamond Powder, Micro-graded Alumina Powder, Cerium Oxide, and other specialized polishing compounds.
Whats Abrasives do we offer & what is the difference between them?
Aluminum Oxide
This is the softest (in relative terms) and most “friable” fused synthetic lapping abrasive we offer. Because of this materials friability it is considered a fine finishing abrasive. In terms of stock removal, aluminum oxide is efficient for cutting materials with a Rockwell “C” scale hardness up to 54. Although, aluminum oxide is sometimes used to process materials harder than 54C to generate a specific surface roughness, it is normally after a roughing step with a more suitable abrasive. There are two forms of aluminum oxide we offer. The most common product is technically called micro-graded dark brown fused aluminum oxide and the other type is micro-graded calcined white alumina.
Calcined Aluminum Oxide
This form of aluminum oxide is recommended for electronic materials processing. The reason for this is the minimal depth of component material subsurface damage created by the more gentle cutting action of this materials non-fused, flat plate like crystals. The cutting action is less stressful because the crystals slide and shave stock from the component instead of gouging a chip of material as a blocky shaped fused crystal does. The flat shape of the crystal helps minimize cutting pressure by contacting more area of the component thus distributing the cutting force over a larger area.
Calcined aluminum oxide is available with and without a suspension treatment. The suspension treatment is a chemical coating of the abrasives individual particles that allows the particles to remain in solution for a longer period when using water as the vehicle. Suspension treated abrasive is not required when lapping with oil or water-base lapping vehicles.
Some users of calcined aluminum oxide are lapping metal components. This is due to scratching problems experienced with the standard fused aluminum oxide. Other customers have reported more scratching problems when using calcined material. This simply points out the fact that every application is different and must be evaluated on its own merits.
Silicon Carbide
This material is considered an aggressive cutting, high stock removal abrasive. It is required to cut materials with Rockwell “C” scale hardness of 55 and higher. Obviously this abrasive can be used to machine softer materials when the surface finish requirement is not so precise. The surface roughness of material processed with a specific grade of silicon carbide abrasive will be higher than those achieved with aluminum oxide of the same particle size. The appearance will be significantly different as well. Aluminum oxide produces a matte finish with very few micro-scratches as opposed to silicon carbide of the same size that produces a very micro-scratched finish.
Boron Carbide
Boron carbide abrasive is an extremely aggressive cutting, ultra high stock removal product. It is recommended only for lapping the hardest materials, generally limited to tungsten carbide and titanium carbide. It is cost prohibitive to use this abrasive for lapping of any other materials due to the exorbitant price of this product.
Diamond
Diamond abrasive is the hardest, most aggressive cutting product we offer. This material is generally used for most machine polishing applications. It is most frequently applied to a soft polishing pad. When diamond is used in a lapping application it is typically used to lap extremely hard materials where high production rates are required. In use, diamond abrasive particles maintain their size because of their hardness and extremely low friability rate. This allows diamond-lapping slurry to be recycled.
Cerium Oxide
This abrasive is used strictly for polishing glass like materials on a soft polishing pad or pitch polishing plate. The average particle size utilized is typically somewhere in the range of one to three microns. Some brands of cerium oxide have a slightly high pH level. These abrasives cause an oxidation of the surface being polished. The oxidized material is mechanically removed by the rotating action of the pitch plate or polishing pad.
Polishing machines utilizing cerium oxide abrasive slurry should be protected from corrosion by using stainless steel components and epoxy paints. The water most commonly used with the cerium oxide is also a source of corrosion for unprotected ferrous metal machine components.